A Major Leap Forward: Organotin Catalyst Breakthrough Enhances PVC Production Efficiency and Reduces Toxicity
Date:2024-04-11 Categories:News
Introduction
Polyvinyl chloride (PVC) is one of the most widely used plastic materials, with applications ranging from construction and packaging to electronics and healthcare. However, the production of PVC involves the use of organotin catalysts, which have raised concerns due to their toxicity and environmental impact. A recent breakthrough in organotin catalyst research offers a potential solution, improving the efficiency of PVC production while reducing toxicity, thereby addressing both industrial and environmental challenges. This article will discuss the significance of this breakthrough, its implications for the PVC industry, and the potential benefits for the environment.
The Role of Organotin Catalysts in PVC Production
Organotin catalysts play a crucial role in the production of PVC, facilitating the polymerization process that transforms vinyl chloride monomer (VCM) into PVC. These catalysts are highly effective in controlling the molecular weight and polydispersity of the resulting PVC, ensuring the desired properties for various applications. However, the toxicity of organotin compounds and their potential to accumulate in the environment have led to increasing regulatory pressure and the search for safer alternatives.

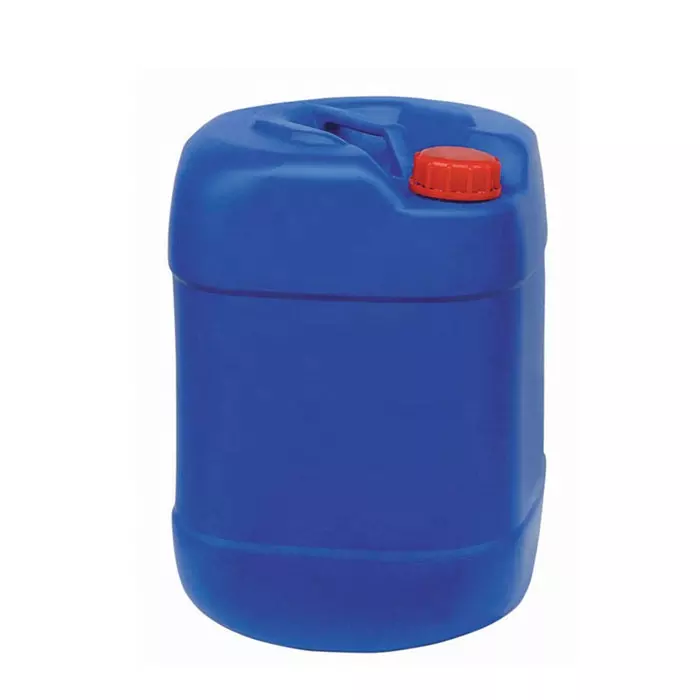
The Breakthrough: A New Organotin Catalyst
A team of researchers has recently developed a novel organotin catalyst that significantly improves the efficiency of PVC production while reducing its toxicity. The new catalyst features a unique ligand design that enhances its stability and selectivity, enabling better control over the polymerization process. This results in the production of PVC with improved properties and reduced waste generation.
Moreover, the new organotin catalyst exhibits lower toxicity compared to conventional organotin compounds, addressing environmental and health concerns associated with their use. The reduced toxicity is attributed to the ligand design, which minimizes the release of toxic byproducts during the catalytic process.
Implications for the PVC Industry
The development of the new organotin catalyst represents a significant advancement for the PVC industry, offering several benefits:
Improved production efficiency: The enhanced stability and selectivity of the new catalyst enable more efficient polymerization, reducing energy consumption and lowering production costs.
Better product quality: The new catalyst allows for better control over the molecular weight and polydispersity of PVC, resulting in improved product properties and performance.
Reduced environmental impact: The lower toxicity of the new catalyst and the decreased generation of toxic byproducts contribute to a more environmentally friendly production process.
Regulatory compliance: As regulations on organotin compounds become increasingly stringent, the new catalyst offers a viable solution for the PVC industry to meet these requirements while maintaining production efficiency.
Potential Benefits for the Environment
The adoption of the new organotin catalyst in PVC production can lead to several environmental benefits:
Reduced toxic emissions: The lower toxicity of the new catalyst can help minimize the release of toxic substances into the environment during PVC production.
Decreased waste generation: The improved efficiency of the polymerization process can result in reduced waste generation, contributing to a more sustainable production cycle.
Lower energy consumption: The enhanced stability and selectivity of the new catalyst can lead to lower energy consumption during PVC production, reducing greenhouse gas emissions and conserving resources.
Conclusion
The breakthrough in organotin catalyst research offers a promising solution for the PVC industry, addressing both efficiency and environmental challenges. By improving the production process and reducing toxicity, the new catalyst has the potential to revolutionize PVC manufacturing, making it more sustainable and environmentally friendly. While further research and development are needed to optimize the new catalyst and scale up its production, this advancement underscores the importance of innovation in addressing industrial and environmental challenges.
Recommended Related Reading:
https://www.bdmaee.net/lupragen-n205/
https://www.bdmaee.net/teda-a20-polyurethane-tertiary-amine-catalyst-tosoh/
https://www.bdmaee.net/teda-l25b-polyurethane-tertiary-amine-catalyst-tosoh/
https://www.bdmaee.net/toyocat-daem-catalyst-tosoh/
https://www.bdmaee.net/toyocat-dmch-hard-bubble-catalyst-for-tertiary-amine-tosoh/
https://www.bdmaee.net/toyocat-dmi-gel-catalyst-tosoh/
https://www.bdmaee.net/toyocat-dt-strong-foaming-catalyst-pentamethyldiethylenetriamine-tosoh/
https://www.bdmaee.net/toyocat-et-catalyst-tosoh/
https://www.bdmaee.net/toyocat-ets-foaming-catalyst-tosoh/
https://www.bdmaee.net/toyocat-mr-gel-balanced-catalyst-tetramethylhexamethylenediamine-tosoh/
https://www.bdmaee.net/toyocat-np-catalyst-tosoh/